GRINDER GR3520 | Rubber Mulch Machine

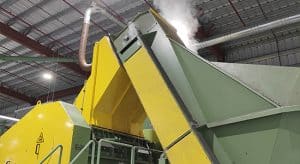
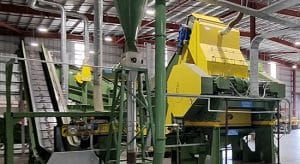
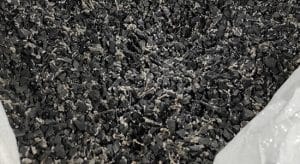
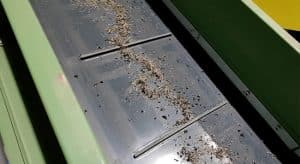
The Grinder GR3520 is a specific machine for the volumetric reduction of shredded waste from end-of-life tyres to producing Rubber Mulch.
It accepts coarse pieces of approximately 100<>350 mm in size per side to reduce it to chip size in dimensions less than 18 mm in apparent diameter.
Below we list the characteristics of the machine.
The aim
Reduce the shredded waste from end-of-life tyres to a particle size of less than 18 mm in controlled grain size.
Free the chopped harmonic steel filaments for the subsequent deferrization phase in the module in which the Granulator is inserted.
Separate by suction the textile dust released by the granulation.
The GRINDER capacity
It has a peak input capacity with 18 mm hole grid of 3,500 Kg/h which in the working cycle of new blades and worn blades stands at an average of 2,800 Kg/h.
Increasing the size of the grid hole results in an increase in productivity at the expense of optimal separation of the harmonic steel filaments.
With its 220 kW of installed electrical power, the automation in regulating the incoming product flows, the machine produces with an absorption of only 0.055 kW/Kg.
The cutting group
Made up of 35 rotating blades with scissor effect cutting configuration, it acts individually on fixed blade sectors to be able to shear the shredded material by exploiting the kinetic energy deriving from the double flywheel transmission.
The blades can be resharpened by removal using a Surface Grinder up to the minimum size declared in the manuals and the cutting clearance adjustments are corrected directly upon reassembly in the machine.
Body machine
Created taking into account any long-term extraordinary maintenance with a simplified method of opening the rotor compartment from above.
The rotor has a long-lasting anti-wear coating on which to reapply coatings in the long term.
Blade holder sectors as well as wear-resistant plates arranged inside the machine are all easily replaceable also thanks to the included supply of the perimeter base for the operator who carries out maintenance.
The machine is served by a customized electrical panel from which the granulation process is controlled by setting the load capacity and thermal control.