Steel Wire cleaning System. The Clean process into tire recycling plant
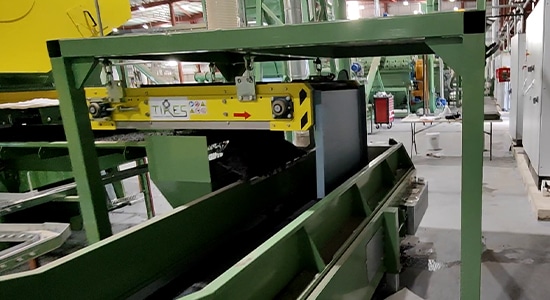
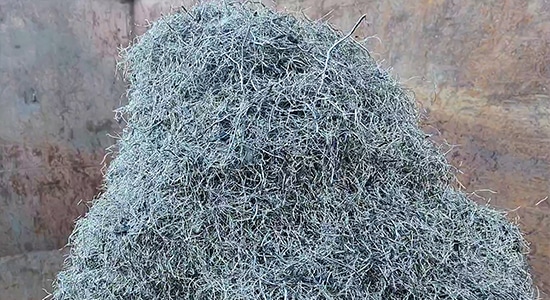
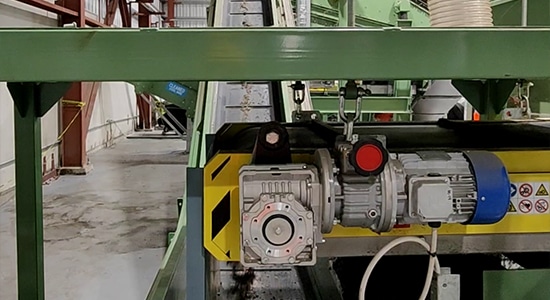
In a tyres recycling plant, production in rubber granules, dirty steel wire and textile fiber, are obtained by separation and must be clean.
A customer who does not already have experience in this sector does not ask himself the question that steel wire may present critical issues on the reuse market.
We at TIRES expose the factual reality in a transparent manner.
The aim to clean
The steel wire cleaning system is an optional module that we at TIRES propose as a solution to significantly reduce the elastomeric fraction present at the exit of the harmonic filaments from the iron remover of a system.
In the case of a TIRES plant, the module called “Clean steel wire system” is connected in a closed circuit with the Grinder Module using low energy consumption and reduced maintenance.
In the case of a plant that does not have a machine inside the Grinder Module capable of accepting an extra quantity of steel filaments at the input, with a well-defined reduced grid, this module can be created separately with integration of the Grinder.
These two case studies are the result of experience where if the technology used has not been engineered to obtain quality results, the economic choice conditions are very different.
The capacities process of Steel Wire Cleaning System
The âClean Steel wire systemâ module allows you to obtain the production of metal filaments with a degree of cleanliness greater than 97% compared to the standard approximately 85% coming out of the Granulation stage.
It involves its acceptability by foundries as a Secondary Raw Material (high price value as per the ferrous scrap stock market index) from its value as waste (low or free price).
In the case of waste, it is also good to know that European foundries do not accept the product due to fume emissions into the atmosphere and therefore the market is only of Asian origin.
The plant can process up to 2,000 Kg/h of passage cycle to obtain the clean harmonic steel fraction deriving from the recycling of end-of-life tires with an energy impact of 0.020 kW/Kg.